Howell Twp. Auto Parts Supplier Deals With COVID Cluster
August 8, 2020
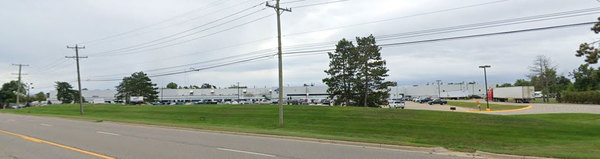
By Jessica Mathews/News@whmi.com
A local automotive supplier is dealing with confirmed COVID-19 cases.
Grupo Antolin is a Tier 1 automotive supplier that operates worldwide and has a facility in Howell Township located at 3705 West Grand River. A concerned employee reached out to WHMI who said they were alerted by telephone messages about confirmed COVID-19 cases, on three separate occasions in July and August.
General Manager Matt Edwards told WHMI their priority is for the safety of employees and they have implemented all required and recommended actions from the Centers for Disease Control, the Michigan Occupational Safety & Health Administration and state executive orders as they relate to manufacturing facilities during the COVID crisis. Just over 600 people are employed at the Howell location. Edwards says there are 6 positive cases and all 6 were communicated to all employees, noting 2 of those cases occurred while the plant was shut down from March to May but they still count them as part of their total. He says each exposed and potentially exposed employee is contacted personally by the company’s HR department.
As for information being disclosed about specific shifts and departments tied to the positive cases, Edwards says that is shared with people who are directly affected by the cases. He says they’re trying to respect the laws of medical privacy with communication to the rest of the employees. Edwards says they’ve been consistent and clear with their message to employees that those who were potentially exposed would be contacted individually. He says the mass callings have been to make sure all employees are informed.
Edwards said they feel that they are leading the way in which they’re handling the pandemic crisis but will not stop challenging their system to be the best that it can be as there are always ways to improve. He provided further information about various safety and training measures that have been implemented to minimize risk and prevent spread, as well as building protocols and additional preventive measures. Those are detailed below:
Training on safe behaviors:
1. All recommended CDC good hygiene practices (Hand washing, social distancing, monitor your health daily, etc..)
2. Hands must be sanitized (provided) before and after using common touch points in the facility.
3. Face mask and/or face shield must be worn at all times. (Except while eating/drinking in designated areas). Proper use of face masks are also touched on during training.
4. Disinfecting work areas before and after use.
5. Maintain an appropriate “social” distance of six (6) feet. (marked on floor in common areas)
Building entry protocol established:
1. Complete the daily health screening PRIOR to entering through the turnstile via smart phone app.
2. Use the barcode received at the completion of the survey to scan in at thermal checkpoint.
3. Go through thermal checkpoint.
a. On successful completion of the thermal scan, the station will print out a label
b. Label must be worn on your person at all times when in the facility.
4. Go through scanning station at end of hallway to make sure label is valid.
Additional preventative actions:
1. Staggered start/break/lunch times to minimize employee exposure and maintain social distancing.
2. Weekly disinfectant fogging of common areas
3. Protective barriers have been installed in break/lunch rooms
4. Doors have been propped open to improve air flow and ease of access through reducing touch points.
5. Door foot openers have been installed and are expected to be used at all times.
6. The frequency of cleaning for restrooms, breakrooms and common areas have been increased. Individual cleaning personnel are assigned to each breakroom on all shifts
7. All common areas have social distancing protocol marked on the floor.
8. Employees will only be permitted to enter the breakroom that is associated with the area in which they are working.
Photo: Google Street View.